Metal Bellows Assemblies
Information at a Glance
Series
7500 Formed Metal Bellows
Material
Steel
Size
1/2 -48 in. / 12-1200 mm
Pressure
≤100, 150 & 300 PSI / 3, 10 & 20 Bar
Motion
unlimited
Canadian Registration
This product is registered throughout Canada under
CRN 0D9278.59870YTNADD3
Other Products
Product Description
Series 7500 formed bellows can be used in assemblies and for applications that are only limited by your imagination. Hyspan is ready to assist you from preliminary design to final testing. The company maintains extensive engineering capability for the design of metal bellows and related hardware, and has complete facilities for prototype production and development testing. Once developed Hyspan has unparalleled capability for volume production at company owned facilities at five locations.
Series 7500 formed bellows can be used in assemblies and for applications that are only limited by your imagination. Hyspan is ready to assist you from preliminary design to final testing. The company maintains extensive engineering capability for the design of metal bellows and related hardware, and has complete facilities for prototype production and development testing. Once developed Hyspan has unparalleled capability for volume production at company owned facilities at five locations.
Valve Seals
Formed bellows are commonly used for packless valve seals in safety, control and high vacuum valves. Hyspan has a complete library of designs for commonly used valves, and the capability to develop new designs. For high temperature and corrosive service speciality alloys such as Monel 400, Alloy 625, and Hastelloy C-276 are available.
Pressure Restrained
Structural components can be added to react the pressure thrust force of unrestrained bellows. In the photograph to the right, gimbal hardware has been added which restrains the bellows but allows universal angular motion. Two or three joints (depending on the application) of this design will absorb linear motion in all directions.
This photograph is an in-line pressure balanced assembly. There are four small diameter which have a total effective area equal to the larger line bellows, and through the rods and structure the pressure thrust is balanced internally. The only resistance to axial motion is the bellows axial spring rate.
Wave Guides
Formed bellows are used as wave guides. The assemblies in the photograph are made from aluminum. As shown they are easily formed into the required shape. Hyspan also manufactures bellows made from stainless steel and Beryllium copper.
Cryogenics and High Vacuum
Probably the most common applications of formed metal bellows are for cryogenic and ultra-high vacuum service. The assemblies shown in the photograph are for cryogenic service in medical equipment. The copper ring in the center is brazed to the stainless steel bellows. The completed assembly is leak tested to 1×10-10scc/sec. of helium. Hyspan maintains ASNT Level II helium leak testing certifications, and has facilities for liquid nitrogen testing.
Volume Compensation and Pressure Actuators
Bellows can be designed into sealed assemblies that can be pressurized internally or externally to provide large volume changes. The exposed bellows is a “crush formed” bellows assembly that was used in an electrical transformer that was designed for a 3x increase in length. The launch pads at Vandenburg AFB use this concept to raise and lower the launch vehicle. The design pressure for this application was 3000 psig.
Development Testing
Hyspan has facilities and equipment for a wide range of testing that is required for bellows product development. The photographs illustrate two bellows designed into a “tied universal”. It was cycled with a lateral offset of 2″ each side of neutral for 22,000 cycles while pressurized to 280 psig and heated to 900°F. The forces and moments at the end attachments were measured during the test.
Hyspan manufactures standard formed metal bellows configurations that are suitable for most applications. Inside diameters range from 1.0″ through 96.0″ with a wide range of material thicknesses, convoluted lengths and materials. Complete technical information is tabulated including design pressure, spring rates and cycle life.
Vacuum Applications
Series 7500 Bellows can be used for high-vacuum applications requiring leakage rates less than 1 x 10-10 STD ATM CC/SEC at base pressure of 1 x 10-6 TORR.

Since most of these applications require extremely flexible bellows, Hyspan recommends materials thickness of 0.006″ for inside diameters (I.D.) up to 4.5″, 0.008″for I.D. up to 8.0″, and 0.010″ for I.D. up to 14″. Any material Thickness can be used which has a maximum pressure (Column 7 on pages 6-17) exceeding 15 PSIG. Type 321 stainless steel is preferred because of its weldability and availability; however, other alloys can be substituted.
Weld attachments for high-vacuum applications are very critical. Because of the thin bellows material that is normally used, the addition of filler rod is not practical. The illustrations show the Hyspan recommended weld joints for internal and external attachments. The bellows must be a tight fit to the band, and the materials compatible because they are fused together.
Beryllium Copper
The beryllium copper alloys have high thermal and electrical conductivity similar to pure copper. It can be readily joined by resistance and fusion welding, brazing and soldering. The material is nonsparking, nonmagnetic; it has high galling resistance, and maintains its strength and ductility at cryogenic temperatures.
Bellows Nomenclature
Bellows Movements
The beryllium copper alloys have high thermal and electrical conductivity similar to pure copper. It can be readily joined by resistance and fusion welding, brazing and soldering. The material is nonsparking, nonmagnetic; it has high galling resistance, and maintains its strength and ductility at cryogenic temperatures.
![]() |
![]() |
![]() |
AXIAL
Extension or compression from the manufactured length along the longitudinal centerline with ends parallel. |
![]() |
LATERAL
Displacement perpendicular to the longitudinal centerline with the ends parallel. |
![]() |
![]() |
![]() |
![]() |
![]() |
ANGULAR Rotation of the longitudinal centerline about the perpendicular axis. |
![]() |
COMBINED Axial, lateral, and angular movements can be combined within the rated movements. |
![]() |
TORSION OR TWISTING AROUND THE CENTERLINE(Not recommended.) |
Standard Tolerances
Inside Diameter | Stock Number | Neck I.D. | Convolution I.D./O.D. | Convoluted Length | Trim Length |
1″-4″ | 7513-7544 | 0.01 | 0.03 | 0.06 | 0.03 |
4.125″-6″ | 7545-7557 | 0.01 | 0.04 | 0.06 | 0.03 |
6.25″-12″ | 7558-7577 | 0.02 | 0.06 | 0.09 | 0.06 |
12.25″-24″ | 7578-7586 | 0.03 | 0.09 | 0.12 | 0.09 |
26″-48″ | 7587-7598 | 0.06 | 0.12 | 0.12 | 0.09 |
50″-96″ | 7599-75110 | 0.12 | 0.18 | 0.18 | 0.12 |
Neck Trims
![]() |
![]() |
![]() |
STANDARD TRIM I.D. NECK The neck and Convolution I.D. are equal to the nominal I.D |
![]() |
STYLE A O.D. NECK The neck O.D. is equal to the convolution O.D. |
![]() |
![]() |
![]() |
STYLE B EXPANDED NECK The neck I.D. or O.D. can be specified within the range of the I.D. to the convolution O.D. |
![]() |
STYLE C O.D. TRIM The trim line is at the tangent point of the convolution O.D. |
![]() |
![]() |
![]() |
![]() |
![]() |
STYLE D I.D. TRIM The trim line is at the tangent point of the convolution I.D. |
![]() |
INSIDE BAND | ![]() |
OUTSIDE BAND |
Series 7500 bellows with Standard, Style A, or Style B neck trims can be specified with inside or outside bands which increase the thickness for welding or added reinforcement. The band thickness is approximately 2.5 times the bellows thickness. The bands are attached by resistance seam welding for sizes 1″ through 48″ and by edge welding (GTAW) for larger sizes.
Caution: The use of bands is not recommended for vacuum applications requiring a mass spectrometer helium leak test. See Vacuum Applications for recommended welding methods.
Multiply or Laminated Bellows
Any standard-size bellows can be fabricated with multiply construction up to four plies of equal thickness. The maximum pressure, spring rate, and stability pressure are increased in direct proportion to the number of plies, but with the same axial deflection as a single ply. Multiply design permits a lower spring rate and a greater cycle life than a single ply configuration for an equivalent pressure. This type of construction is recommended for applications with vibration or rapid cyclic motion because of the inherent damping provided by the relative movement of the plies. Multiply construction in not recommended for vacuum application requiring a mass spectrometer helium leak test because of possible out-gassing from an undetectable leak in an inner ply.
Refer to the individual topics in the Explanation of Tabulated Data for the methods used to calculate multiply bellows parameters.
All dimensional data is applicable to tabulated single and multiply configurations with standard and optional materials. The tabulated performance parameters are for type 321 stainless steel at room temperature; however, they apply to all austenitic stainless steels with minor variations. Variations for other materials are given for each column explanation.
Materials & Properties
The performance data tabulated in Columns 7 through 11 (pages 6-17) was calculated for type 321 stainless steel at 70ºF. These values are a function of the Modulus of Elasticity, strength, and fatigue life. If the service conditions are substantially different or an optional material is used, contact the factory for assistance.
Optional materials can be substituted which include but are not limited to alloys 600, 625, 800, 825, Cb-20 and C-276, Nickel 200, Beryllium Copper and weldable Aluminum alloys.
Use of Tabulation
The data included in this catalog was computed by generally accepted analytical methods and empirical data derived from tests. This data should be used as a design guide only. Consult the factory if you have an application requiring close control of these values.
The following paragraph numbers refer to the column numbers of the tabulated data on pages 6 through 17.
- Stock Number
A four or five digit number identifies the nominal size (inside diameter), and a letter corresponds to the material thickness. In order to fully specify the desired configuration refer to the Ordering Instructions on page 18. - Inside Diameter
Nominal Inside diameter of the convolutions and the standard neck trim. - Convolution Outside Diameter
Nominal outside diameter of the convolutions and maximum diameter of Style A neck trim. - Effective Area
The cross-sectional area of the bellows based on the mean diameter of convolutions. This area multiplied by the pressure equals the pressure thrust force (Lbs.). - Material Thickness
The values tabulated are representative designs for each diameter. Other thickness may be available – consult the factory. - Maximum Convoluted Length
These values are established by manufacturing limitations. Substantially longer lengths must be obtained by splicing two or more elements. Any shorter length can be specified – refer to the Ordering Instructions. - Maximum Pressure
The highest internal or external pressure recommended with a corresponding test pressure of 1.5 times this value. This pressure is exclusive of the squirm or instability pressure (Column 8).The working pressure for internally pressurized bellows is determined from the pressure tabulated in Column 7, or the squirm pressure calculated from Column 8 – whichever is lowest. For convenience Column 7 and 8 include a test pressure factor of 1.5, i.e., a bellows can be pressurized to 1.5 times the pressure tabulated in Column 7 without permanent set, and the anticipated squirm pressure is greater than 1.5 times the value calculated from Column 8. The working pressure for internally pressurized bellows which are guided or supported to prevent squirm is determined from Column 7.The working pressure for externally pressurized bellows is determined from Column 7 – squirm or instability does not occur. All bellows rated at a pressure (Column 7) exceeding 15 psi are satisfactory for Full Vacuum (internal) applications – Caution – This pressure applies to the convoluted sections only and the standard neck trims. Long unsupported neck trims may collapse. Multiply or Laminated Construction – multiply the values of Columns 7 and 8 times the number of plies. - Squirm or Instability Pressure
Internally pressurized bellows are unstable at the critical or squirm pressure. In most instances this condition is characterized by the centerline of individual convolutions deviating from a common centerline – analogous to buckling of a long column under compression. This condition occurs when the convoluted length is long relative to the inside diameter – over 2 or 2.5 times. There is also a less familiar type of squirm which occurs when the plane of the individual convolutions deviates from parallel planes. Either condition represents a maximum pressure and failure will occur if pressure is increased.The tabulated values (Column 8) are the maximum recommended internal pressure to avoid squirm for one inch of convoluted length. The values are based on a test pressure 1.5 times the tabulated pressure. The pressure for other lengths can be calculated by dividing the tabulated value by the square of the convoluted length.The Column 8 values do not need to be corrected for other materials which have a modulus of elasticity in the range of 28 – 30 x 106 psi. For multiply construction multiply the tabulated value by the number of plies. - Axial Spring Rate
The force (Lbs.) per inch of axial extension or compression resulting from the material and configuration spring constant is tabulated for one inch of convoluted length. The spring rate for other convoluted lengths is determined by dividing the tabulated values by the convoluted length. Multiply this value by the number of plies for multiply construction. - Lateral Spring Rate
The force (Lbs.) per inch of the lateral offset resulting from the material and configuration spring constant is tabulated for one inch of convoluted length. This movement occurs when the ends remain parallel to each other and perpendicular to the longitudinal centerline, but the centerline displaces laterally. The lateral spring rate for bellows other than one inch convoluted length is calculated by dividing the cube of the convoluted length. For multiply construction multiply by the number of plies. Caution – The tabulated values must be multiplied by the 1000 except as noted to obtain the true spring rate. - Axial Deflection
The allowable axial extension or compression for one inch of convoluted length is tabulated for 2000 cycles of movement from the nominal length to the tabulated value. The movement for other convoluted lengths are obtained by multiplying by the required length. Since these values are determined by the metal fatigue due to the bending stress produced by movement it is unchanged for multiply construction.
The tabulated values can be corrected for other numbers of cycles (at 70ºF.) by applying the following factors:
![]() |
![]() |
500 | 1.40 |
1,000 | 1.20 |
2,000 | 1.00 |
4,000 | 0.85 |
8,000 | 0.75 |
10,000 | 0.70 |
Hyspan Series 7500 Formed Bellows may be ordered directly from this catalog by using the stock number selected from the tabulation and adding the appropriate Dash Numbers.
If the neck trim length is deleted from the part number it is assumed to be the standard—0.75″ through 6″ I.D., 1.0″ over 6″ I.D. Optional materials, neck trim configurations, and bands must be specified separately—refer to pages 3 and 4 for options available.
Example
Size: 1.50″ I.D., 1.95″ O.D.
Material: .008″ Thick Type 321Stainless Steel
Convoluted Length: 4.0″
Neck Trim: 0.50″
Hyspan products are available from Sales Representatives and Distributors, or they can be purchased direct from the factory. The minimum factory order for open account customers, COD shipments, or bank card sales is $50.00 (USD). All major credit or debit cards are accepted. The minimum order for new account applicants is $500.00. Our Confidential Credit Application can be downloaded and forwarded to Hyspan for processing. All orders are subject to the following Terms and Conditions, and the following warranty applies to all material. Please read these documents.
Hyspan products are available from Sales Representatives and Distributors, or they can be purchased direct from the factory. The minimum factory order for open account customers, COD shipments, or bank card sales is $100.00 (USD). All major credit or debit cards are accepted. The minimum order for new account applicants is $100.00. Our Confidential Credit Application can be downloaded and forwarded to Hyspan for processing. All orders are subject to the following Terms and Conditions, and the above warranty applies to all material. Please read these documents.
Confidential Credit Application (13.9 KB), can be completed on line.
This warranty is given by Hyspan Precision Products, Inc. (Hyspan), located at 1685 Brandywine Avenue, Chula Vista, California 91911, (619) 421-1355, for the benefit of the first purchaser of the product to which the warranty applies. This warranty applies to those parts which are manufactured and delivered by Hyspan.
The warranty is that the parts manufactured and delivered by Hyspan will be free from defects in material or workmanship under normal use and service for the time specified below.
In the event of failure of a part due to such a covered defect, Hyspan will repair or replace, at its option, the defective part at its factory located at 1685 Brandywine Avenue, Chula Vista, California 91911.
The part must be returned to the factory by and at the expense of the person claiming the benefit of the warranty.
The warranty shall be for a period of twenty-four (24) months after the date of delivery of the product, twelve (12) months after commencement of use of the product, whichever period is the shortest. All products for which warranty claims are made must be returned as provided above to the factory within thirty (30) days from the date of claimed malfunction in order for this warranty to be effective. The only entity authorized to do any warranty repairs is the manufacturer.
The repairs or replacement by Hyspan will be accomplished within forty-five (45) days from receipt of the defective parts at the factory.
This warranty is expressed in lieu of all other warranties, expressed or implied, including the warranty of merchantability, the implied warranty of fitness for a particular purpose, and of all other obligations or liabilities on the part of Hyspan, and it neither assumes nor authorizes any other persons to assume for Hyspan any other liabilities in connection with the sale of the products.
This warranty does not cover parts of products made by others or products or any part thereof which have been repaired or altered, except by Hyspan, or which shall have been subjected to misuse, negligence, or accident.
Hyspan shall not be liable for damage or delay suffered by the purchaser regardless of whether such damages are general, special, or consequential in nature, whether caused by defective material or workmanship or otherwise, or whether caused by Hyspan’s negligence regardless of the degree.
- Orders. Orders are subject to acceptance at the home office of the seller.
- Assignment. Purchaser may not assign this Agreement without Hyspan’s prior written consent.
- Written or Typed Provisions Govern. In the event of a conflict between any of the printed provisions hereof and any written or typed provision hereof, the written or typed provisions shall govern. Clerical and stenographic errors are not binding and may be corrected by Hyspan at any time after discovery.
- Designs. All designs and specifications shown in seller’s catalog are subject to change without notice.
- Liability. The buyer shall remain primarily liable for the purchase price, and the seller shall not be obliged to accept any term or condition of payment which would shift said liability to a third person not a party to the contract of sale, whether or not such third person is the United States Government, its agents or instrumentalities.
- Weights and Dimensions. Shipping weights and dimensions given in seller’s catalog are as close to actual as practicable but are not guaranteed. No claims shall be allowed because of any discrepancy between actual weights or dimensions of material shipped and listed data.
- Shipping and Packing. All material is carefully packed for shipment, and seller shall not be responsible for loss, delay or breakage after having received “in good order” receipts from the transportation company. All claims for breakage, loss, delay and damage should be made to carriers, but seller shall render buyer all possible assistance in securing satisfactory adjustment of such claims. In the absence of directions, goods shall be shipped by the method and via carrier seller believes dependable. Goods held in factory beyond delivery date for convenience of buyer shall be invoiced on date of completion and terms of payment shall apply as from invoice date. Such goods shall be subject to charges for warehousing and other expenses incident to such delay.
- Cancellation. Orders are not subject to cancellation or change in specifications, shipping schedules or other conditions originally agreed upon without seller’s consent, and then only upon agreement to compensate seller for loss caused by such cancellation or changes.
- Cost Analysis. No cost analysis of the cost of manufacturing the equipment sold shall be supplied, and no examination or audit of the seller’s books and records shall be permitted for any reason whatsoever.
- Compliance with Laws. Seller has complied with all applicable Federal, State and local laws and regulations in connection with the manufacture and sale of all equipment. No responsibility or liability shall be taken for import duties, laws, regulations or taxes imposed by any foreign country.
- Taxes. Any manufacturer’s excise tax, use tax, sales tax, or tax or duty of any nature whatsoever arising out of or assessed against orders, shall be added to the prices quoted or invoiced and shall be paid by the buyer; in the event seller is required to pay any such taxes or duties, the buyer shall reimburse seller therefore, unless buyer shall provide seller at the time an order is submitted with exemption certificates or other documents acceptable to taxing or customs authorities.
- Shipping Date. Seller shall not be liable in any way for any default or delay in shipping due to contingencies beyond its control, or the control of its suppliers or sub-contractors, which prevents or interferes with the seller making delivery on the date specified. In the event of delayed or extended shipping dates, and the buyer changes shipping instructions, any additional shipping charges shall be paid by the buyer as a part of the purchase price.
- Returns for Credit. No returns for credit shall be accepted unless seller’s permission has been obtained in each case in advance. Only sizes and designs taken from seller’s regular line which are in active demand can be accepted for credit. Credit shall based on prices prevailing at the time of return, or invoiced price, whichever is lower, subject to deduction for handling and an additional deduction for expenses incurred in restoring goods to salable conditions. Obsolete or specially manufactured goods can be accepted for return or credit only to the extent of value to seller in each case. No credit shall be issued to other than the original purchaser.
- Risk of Loss. Risk of loss shall pass to the buyer upon delivery to the transportation company. If goods are held in the factory beyond the shipping date for buyer’s convenience, the risk of loss shall pass to the buyer upon the date originally scheduled for shipping. The buyer shall pay all costs of insurance from the time the risk of loss passes to the buyer.
- Interest. In the event that buyer has not tendered payment within the time set forth in the order, seller may charge the buyer interest on the then due amounts until payment is actually received by seller. The interest rate shall be 1.5% per month. The right of seller to charge such interest is in addition, and not in lieu, of any other right the seller may have against the buyer for breach under a sales agreement.
- Shipping Costs. Unless otherwise specified, buyer shall pay all costs of shipping. Seller’s sole responsibility shall be to deliver the goods to the shipper at seller’s factory.
- The Warranty. The sole warranty applicable to goods manufactured or sold by seller shall be the limited warranty which is incorporated herein.
- Attorney’s Fees. In the event either party is required to bring an action in connection with these terms or conditions of sale, or any action in connection with collection of amounts due hereunder, the prevailing party shall be entitled to recover all of its costs or expenses, including reasonable attorney’s fees.
- Applicable Law. This agreement shall be constructed in accordance with the laws of the State of California in effect on the date hereof. The parties agreed that the proper forum for any action pursuant to this agreement is by the State of California, County of San Diego.
- Price changes. In the event any prices are not set forth in seller’s Marketing Handbook or catalog, such prices are subject to change without notice.
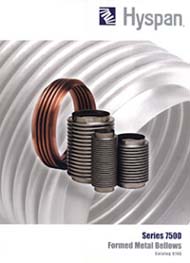
Downloads
- Full Catalog
- Tabulated Design Data (pdf files)
– Inside Diameters 1.0″ through 3.5″
– Inside Diameters 3.625″ through 7.0″
– Inside Diameters 7.5″ through 20.0″
– Inside Diameters 22.0″ through 96.0″
- Tabulated Design Data (pdf files)